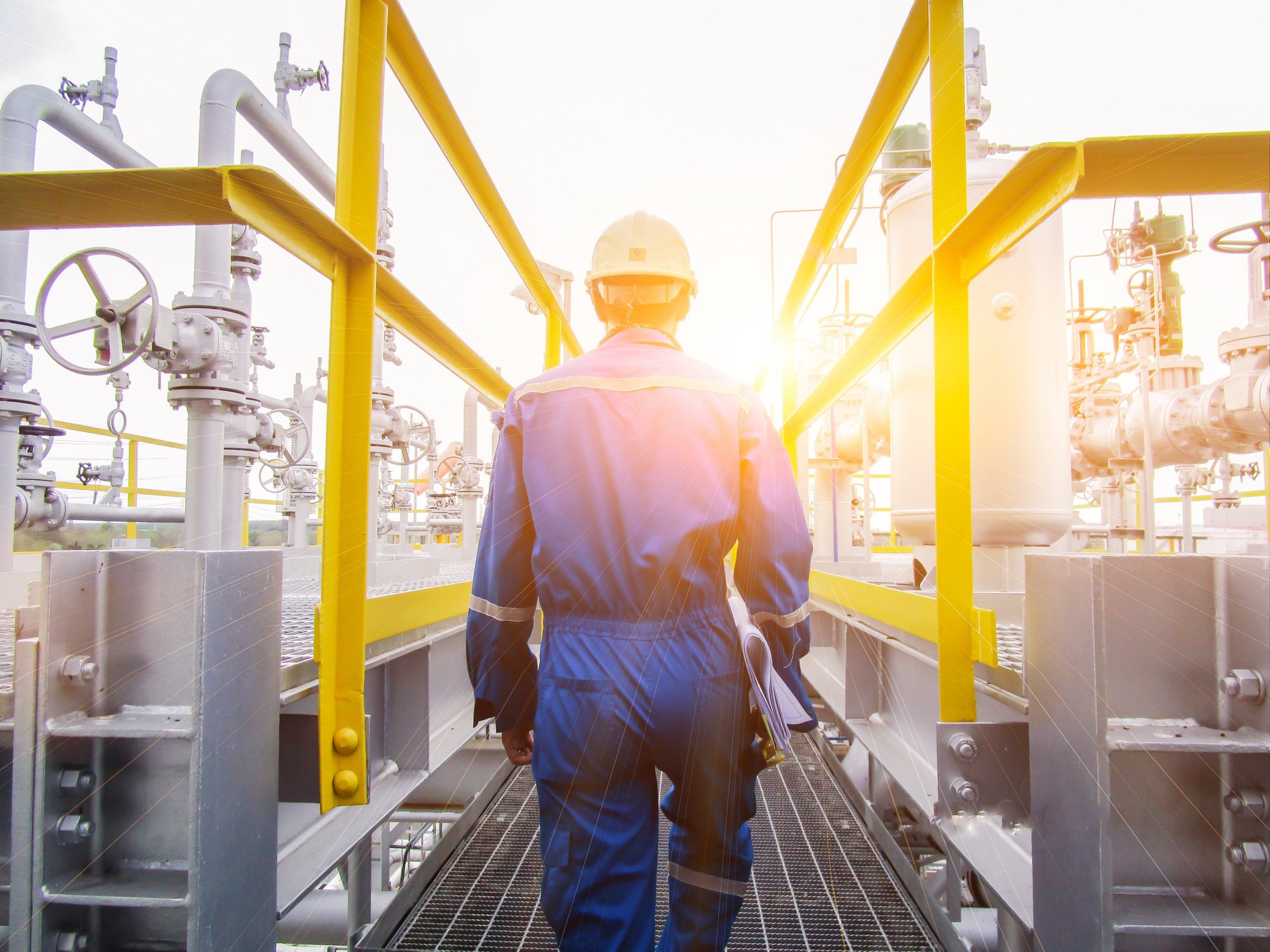
Revolutionizing Frontline Training:
Denbury’s Skyllful Solution for Sustainable Success
Discover how Denbury revolutionized frontline training with Skyllful, enhancing efficiency and sustainability through innovative digital transformation.
Denbury Fast Facts
Year Founded
Employee Count
Annual Revenue
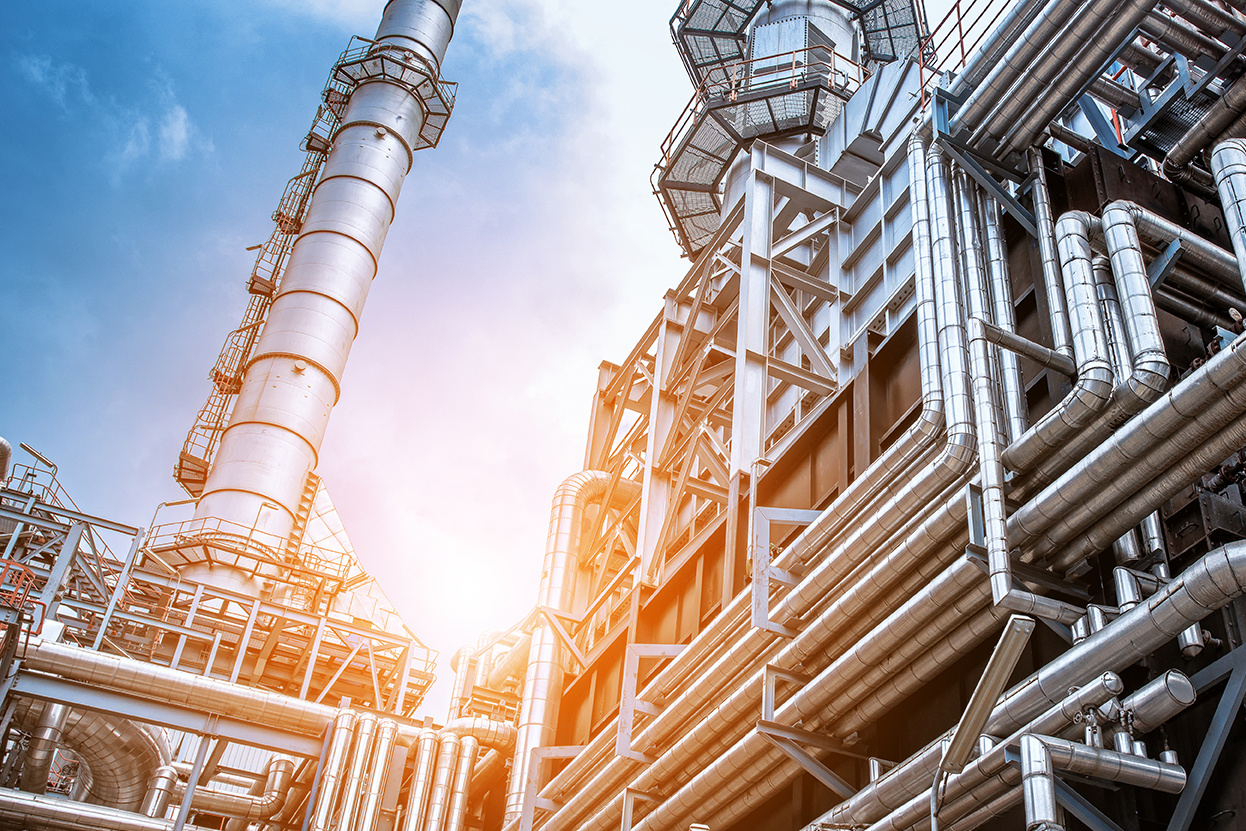
The Background
Turning carbon into clean energy for more than two decades, Denbury Inc. owns and operates the world’s largest CO2 pipeline network, with extensive experience managing CO2 transportation, injection, and monitoring. Focused on the development of enhanced oil recovery (EOR) and carbon capture, utilization, and storage (CCUS) operations in the Rocky Mountain and Gulf Coast regions, Denbury—a Plano, Texas-based oil and natural gas producer since the early 1990s—is committed to carbon management.
Since 2012, Denbury has been active in CCUS through the injection and repurposing of captured CO2 emissions and prioritizes utilization of CO2 in its EOR operations. Sustainability is central to Denbury’s business; continuously innovating to meet the world’s energy needs is essential to its vision for industrial decarbonization. As such, the company is in the midst of a digital transformation journey—one that took a high-profile step forward with the announcement that ExxonMobil had entered into a definitive agreement to acquire Denbury, part of its plan to accelerate its low carbon solutions business and play a greater role in a sustainable energy transition.
A leader in CCUS, Denbury’s EOR operations prevent CO2 from polluting the atmosphere by recycling CO2 to produce carbon-negative Blue Oil. Its 1,300 miles of pipelines that transport CO2 represent key infrastructure that can be used to achieve ExxonMobil’s sustainability mission: net-zero emissions by 2050.
What was really unique about Skyllful, that stood out, was that they
had a real passion and drive for customer success.
Get Access to the full Denbury Case Study
The Initiative
Accurate Inventory Management
Maintenance, repair, and operations (MRO) processes are standard for any manufacturer, which needs to have spare parts available to continue operating smoothly in case—or when—something breaks. However, managing inventory by hand at GCC led to inaccuracies between what was entered into their system and what the mechanic actually wrote down. Inventory reporting discrepancies and managing spare parts presented a challenge for GCC, especially due to its already large footprint and rapid growth throughout Latin America and North America.
To avoid any delays in the supply chain resulting from a spare part not being available, GCC simply stocked additional parts. While this is one solution to keeping a plant running smoothly, having too many spare parts on hand can lead to unnecessary redundancies and costs, not to mention the oversights that are likely to occur, such as failing to order a part or being unable to keep track of where existing spare parts reside in a sprawling warehouse.
GCC needed to have an appropriate amount of spare parts on hand, know where to find them, and begin to automate processes.
The Skyllful team was able to adapt, put the training in the end-users’ hands, and empower them wherever they were.”
The Solution
Training With App Simulations
To revolutionize frontline training at Denbury, IT and training leaders selected Skyllful, an end-to-end mobile app simulation platform that specializes in helping businesses navigate the technology adoption lifecycle and empower large, mobile workforces to deploy mission-critical enterprise applications smoothly and successfully.
At the core of Skyllful’s technology is an application simulator optimized for frontline systems training, which teaches users how to navigate and use the essential enterprise applications required for them to do their jobs with variable types of learning and knowledge confirmation.
Interactive Training
To emulate the experience of hands-on learning in a controlled environment that simulates real-world activities, Skyllful delivers high-fidelity simulations and lessons customized with business context, allowing learners to build proficiency with technology platforms and applications that directly support their relevant workflows.
Micro-Learning Content
To avoid overwhelming frontline workers and improve long-term knowledge retention, learners can gain proficiency through short, self-guided, micro-learning app simulations that prioritize the right lessons at any time or place.
Mobile Delivery
To ensure field technicians can further learn in the field and refresh their knowledge whenever necessary in the flow-of-work, app simulations can be accessed from their primary mobile devices and downloaded for offline access, whether they are in transit, at field stations, or at wellsites.
Optimized Content Authoring Tools
Skyllful’s SaaS platform offers customers the ability to easily capture app screens and workflows; edit and change screen text; create high-fidelity simulations; and produce multiple modes of learning, including videos, walkthroughs, practices, and knowledge checks. Content can be designed for consumption on different mobile devices and form factors.
Through Skyllful’s IQ analytics dashboard, training managers can monitor employee progress in real-time, enhancing the quality of learning and enabling continual skills assessment. Additionally, Skyllful collaborates with subject matter experts to create all the simulator lesson content needed for systems training, emphasizing hands-on learning and diversity of content structure, from written guides to short-form videos to walkthroughs.
Skyllful was implemented at Denbury in the span of five months; the initial roll-out involved 400 users across multiple states in the U.S. The company’s project management process first involved creating a functional specification for Skyllful and involved operators, technicians, and other stakeholders in the design and development phase, to create a shared sense of ownership while creating champions to lead the effort in the field. “We were building a sense of excitement from both the top and the bottom of the business,” Brown said.
In piloting the platform across different fields, Denbury’s team made the business case for Skyllful to each group of employees leveraging it, so that every individual understood the value that it would unlock for their job roles. While cost savings and improved data integrity were important goals for the business to achieve, Brown knew that the success of Skyllful would also be measured by individual adoption of the training platform.
The more likely it is that they’re going to be confident when they go out there and do their jobs, the more likely it is that they’re going to be thinking about what really matters: safety, the task at hand, and keeping all their fingers and toes.
The Results
Increased Technology Adoption
After implementing Skyllful at Denbury, training managers saw an 85% adoption rate within the first three months of rolling out the technology. Additionally, employee surveys continually assessed whether individuals were unlocking value from Skyllful; 97% of survey respondents said that Skyllful “made their jobs easier,” according to Brown.
Training Time Reduction
Additionally, Denbury saw substantial time reductions in SAP training efforts. Previously, the complexity of SAP systems in use at Denbury was such that all-day training was required to bring technicians up to speed on the systems, and another 4–6-month period was typically needed to ensure technicians understood their responsibilities. With technicians benefitting from the simplified accessibility of Skyllful’s curriculum, Denbury has since reduced that training time to three hours.
Increased Employee Confidence
“Skyllful gives our technicians an opportunity to build their confidence before they go out into the field and do it for real,” Brown said, noting the relevance this holds for ensuring the safety of Denbury’s employees. “The more likely it is that they’re going to be confident when they go out there and do their jobs, the more likely it is that they’re going to be thinking about what really matters: safety, the task at hand, and keeping all their fingers and toes.”
Brown added: “That’s because they’re not intimidated by this new tool we’ve decided to put in their hands, having gone through all the walkthroughs and had opportunities to fail and succeed before they’ve had to go out there and really do their jobs. It gets their heads in the right place and makes them feel they have the resources they require to tackle any new tasks. They have everything they need, a click away.”
People are afraid of change because they’re afraid of failure. Skyllful succeeds because it puts the ownership of training in the user’s hands. The end user is empowered to take control of their own training and development.
Lessons Learned
Reduced Need For External Training
Brown now cites Skyllful as “the best value of any investment” he’s overseen in his time at Denbury, quoting the reduced need for external training resources and improved change management as two areas through which the technology has empowered the organization.
Increased Data Integrity
Additionally, data integrity has noticeably improved at Denbury, particularly in terms of capturing failure codes, with all technicians now following a shared set of steps to troubleshoot systems and navigate process flows. In the enhanced training environment, the Denbury team’s capability for self-service learning has increased exponentially.
For Denbury, the improvements Skyllful enabled for their training processes were extensive, from interactive simulated content and content-creation services to enhanced managerial oversight and dashboard visibility. Through this transformation, highly distributed workers became accustomed to hands-on learning, allowing them to simulate workflow steps before implementing them in the field—and resulting in game-changing customer service for the organization.
But Denbury could not have succeeded in implementing Skyllful without an innovative, digital-transformation mindset taking hold for both IT and business stakeholders. “Any technology project that you roll into the frontline can’t singularly be an IT project,” said Brown. “It has to be a business-driven project. Everyone has to buy-in upfront, because otherwise they’re not motivated to help the project succeed.”
As Denbury’s training managers discovered, change management is a non-negotiable component of any technology modernization project, and success requires the project’s stakeholders to first understand, then address any internal resistance to progress.
Goals Accomplished
Finally, the Skyllful implementation has moved Denbury closer to its overall goals of digital transformation and internal upskilling by enabling individuals within the organization to update and enhance mobile training rather than relying on costly external resources.
Soon, other teams within Denbury took notice, from accountants to budget owners and project owners. “Everybody saw the benefit of it,” added Justin Lester, Director of Supply Chain Management (SCM) and Enterprise Asset Management (EAM). “Skyllful has spread like wildfire through the organization.”
Recently, accountants rolled out a new invoicing solution and, rather than host a formal training, built out a curriculum on Skyllful, emailed the link to it around the organization, and effectively upskilled 500 users through this mobile training solution.
Skyllful’s widespread adoption in Denbury opened new avenues for addressing knowledge gaps and acquiring information while consolidating them into a single accessible pathway. “You have to make sure you overcommunicate what the path for help is,” said Brown. “Your first stop is Skyllful, your second stop is your power users, the third stop is IT, and then after that it would be the vendor that helped us develop the application.”
Everybody saw the benefit of it. Skyllful has spread like wildfire through the organization.
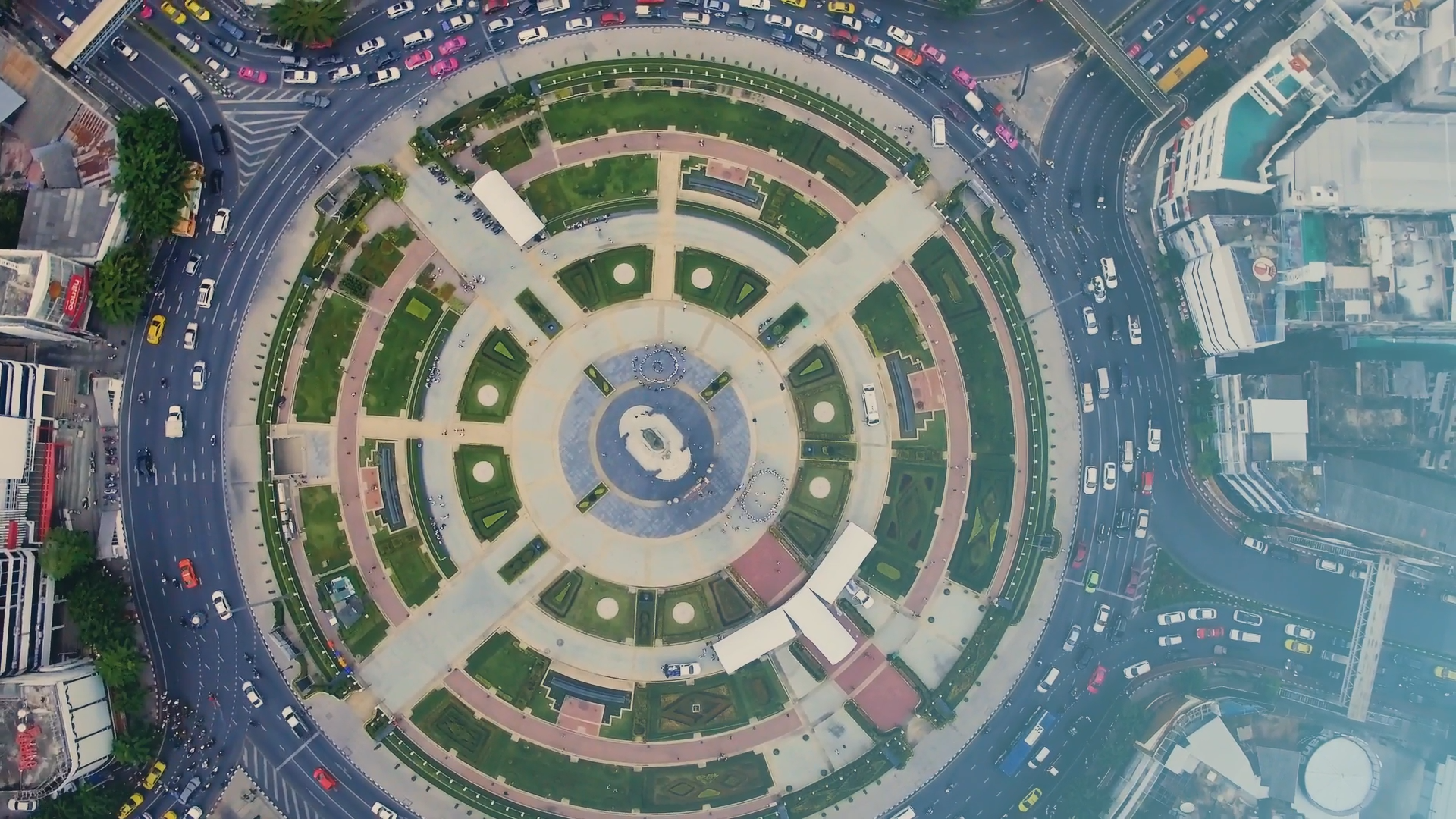
Get Access to the full Denbury Case Study
Denbury Inc., a Plano, Texas-based oil and natural gas producer specializing in enhanced oil recovery (EOR) and carbon capture, utilization, and storage (CCUS), was recently acquired by ExxonMobil to accelerate low carbon solutions and support a sustainable energy transition. With over two decades of experience, Denbury operates the world’s largest CO2 pipeline network, focused on sustainable carbon management and industrial decarbonization.